化工行业作为我国的传统行业在国民经济中占有重要地位。2020年,我国化工生产企业达到30万个,其中八成的个体化工企业抵御风险能力弱。而化工企业属于技术密集型企业,工艺复杂,各生产单元联系紧密,设备、管道密集,工艺条件苛刻。这些特点决定了化工生产过程发生事故的可能性大,造成的人员财产损失更大。为避免类似江苏盐城重大安全事故的发生,一方面企业员工的安全意识、安全职责亟待提高,更重要的是利用智能技术,在早期发现、识别异常工况并提早处置,起到把控工艺流程的风险的作用。
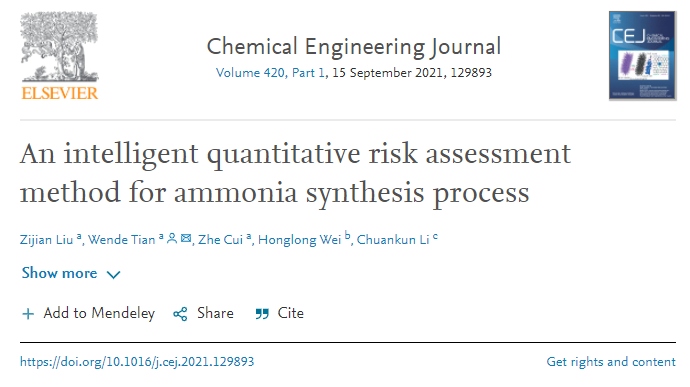
近日,青岛科技大学田文德教授团队报道了关于化工安全故障预测和诊断的相关进展。利用深度学习、定量风险评估、贝叶斯网络等方法在化工工况风险预测、故障诊断等方面取得突破,并在国际知名学术期刊Chemical Engineering Journal(一区TOP,IF=13.273)上发表了两篇题目分别为“An intelligent quantitative risk assessment method for ammonia synthesis process”和“Optimized principal component analysis and multi-state Bayesian network integrated method for chemical process monitoring and variable state prediction”的文章。
其中,文章“An intelligent quantitative risk assessment method for ammonia synthesis process”针对动态化工过程潜在风险难以预测的情况提出了一种智能的定量风险评估方法(如图1),通过深度学习技术捕捉工艺变量的深层特征,评估工况的风险等级,最终制定控制方案,保证工艺的安全运行。文章“Optimized principal component analysis and multi-state Bayesian network integrated method for chemical process monitoring and variable state prediction”针对化工企业异常工况根原因追溯困难的实际难题,提出了一种先进的过程监控方法(如图2),通过改进PCA以及构建新型多状态贝叶斯网络,做到全面的故障传播路径分析,保障化工企业的安全生产以及异常工况的提早处置。两篇文章均以青岛科技大学为第一单位,皇冠hg1088官方田文德教授为论文的通讯作者,博士研究生刘子健、硕士研究生柳楠分别为两篇论文的第一作者,实验室老师刘彬、李传坤、崔哲参与指导工作。
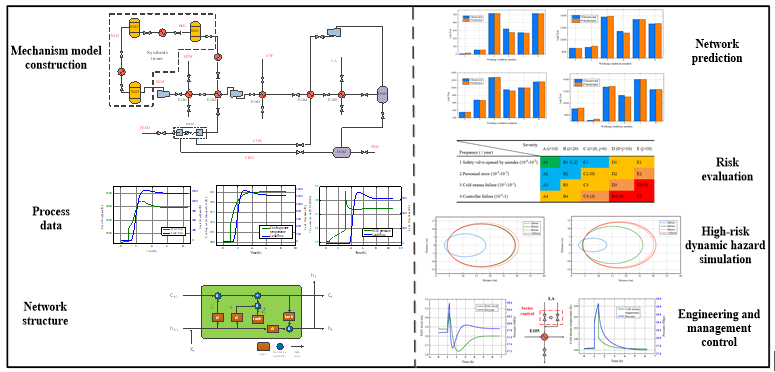
图1.智能定量风险评估方法思路框图

图2. OPCA-MBN变量状态预测与工程监控思路框图
以上工作得到了国家自然科学基金和山东省重大科技创新工程项目的支持。
论文链接:https://doi.org/10.1016/j.cej.2021.129893
https://doi.org/10.1016/j.cej.2021.132617